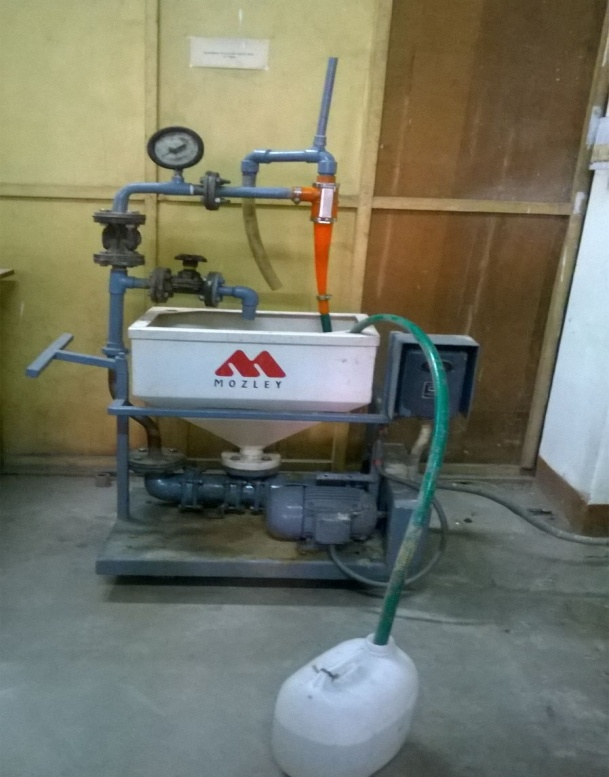
Development of suitable slime waste management systems for sustainable iron mining in India
Dr. Sudipta Mukhopadhyay
Department of Mining Engineering
Indian Institute of Engineering Science and Technology, Shibpur
Characterization of the iron ore lump, iron ore fine and iron ore slime from Donimalai Iron ore deposits, situated in the Bellary district – state of Karnataka, India, belonging to the National Mineral Development Corporation (NMDC Ltd.) was studied. The processing of iron ore using the wet processing method produces a larger amount of micro fines, which were currently discarded as waste due to the presence of large amounts of Silica and Alumina as gangue minerals than their permissible limit, i.e. according to Indian context less than 2% alumina and silica level can be directly fed into the blast furnace. Iron ore with above the desirable limit of alumina and silica can be beneficiated or discarded as waste. The present research work is to characterize the slime which was currently discarded as waste and to evaluate the beneficiation prospective of Iron ore slime. The slime from the tailing dam were collected and processed, and subjected to XRD (X-ray diffraction) analysis, SEM-EDS (Scanning Electron Microscope - Energy Dispersive Spectroscopy) analysis and quantitative mineralogical assessment using potassium dichromate test and ICP-AES (Inductive Coupled Plasma Spectroscopy- Atomic Emission Spectroscopy) analysis. The micromorphology study of the iron ore with its corresponding chemical composition was found out using SEM-EDS analysis. From which we can able to find the liberation characteristics and mineralogical texture which helps to develop a proper beneficiation flow sheet. Followed by the potassium di chromate test and ICP-AES analysis the Fe (iron) % has found to be ranging from 49.60-56.3%whereas the alumina (Al2O3) ranges from5.85 -9.07%, in case of Silica (SiO2) it ranges from 10.10-13.20%. From this we can able to see there is a maximum existence of iron bearing phase, i.e. hematite in the slime, which we are currently discarding as waste. Those slimes can be utilized like iron ore after subjected to the proper beneficiation technique. The current research opens a wide idea about the need of beneficiation for the low grade iron ore slime and exploring the possible ways for industry to attain the zero waste production and also opens wide research topics on mineral processing and waste management.